Distilled Spirits Plant Permit
What is a DSP Permit?
A Distilled Spirits Plant Permit, or DSP Permit, is a federal license issued by the Alcohol and Tobacco Tax and Trade Bureau (TTB) that allows businesses to legally produce, store, bottle, or process distilled spirits in the United States. This permit is essential for distilleries of all sizes, ensuring compliance with federal laws and regulations that govern the production and distribution of spirits like whiskey, vodka, gin, rum, and other liquors.
What Does a DSP Permit Regulate?
The Distilled Spirits Plant Permit oversees multiple aspects of distillery operations, including:
- Production: Ensures the lawful manufacturing of distilled spirits, from fermentation to distillation.
- Processing: Regulates activities such as blending, flavoring, and packaging of spirits.
- Storage: Sets standards for storing spirits in bonded warehouses and maintaining inventory controls.
- Tax Compliance: Monitors the accurate calculation, reporting, and payment of federal excise taxes on distilled spirits.
- Recordkeeping: Requires detailed tracking of production, storage, and sales to ensure transparency and prevent fraud.
- Labeling: Verifies that product labels comply with federal requirements, including proof statements, ingredient disclosures, and origin designations.
The DSP Permit ensures that distilleries operate safely, transparently, and in compliance with federal standards.
Why Do You Need a Distilled Spirits Plant Permit?
If you intend to produce, bottle, or distribute distilled spirits, a DSP Permit is legally required before beginning operations. Without this permit, your business cannot legally function, and non-compliance can lead to substantial penalties, product confiscation, and even business closure.
A DSP Permit not only keeps your business compliant with federal laws but also ensures you are operating ethically and meeting industry standards. It builds trust with distributors, retailers, and customers, demonstrating your commitment to safety and quality.
Whether you’re launching a craft distillery, expanding your spirits business, or engaging in contract distillation, obtaining a DSP Permit is a critical step in building a successful and lawful operation in the spirits industry.
Contact Clear Beverage Licensing Today to Get Help with Your DSP Permit.
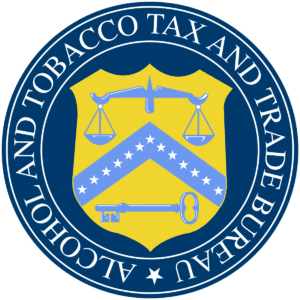
Distilled Spirits Plant Permit FAQ
A distilled spirits plant permit is a legal authorization issued by regulatory bodies (such as the Alcohol and Tobacco Tax and Trade Bureau in the U.S.) that allows a business to legally manufacture, store, and distribute distilled spirits. This permit ensures that the production process complies with federal, state, and local laws regarding taxation, safety, and quality control.
Applicants typically must have an established business entity and secure production facilities that meet specific safety and security standards. Detailed information about the planned operations, facility layout, and production methods is required. Financial stability and background checks are also common prerequisites to ensure the applicant’s ability to comply with ongoing regulatory obligations
The application process generally involves completing the appropriate forms and submitting comprehensive documentation regarding your business, facility, and production plans. This may include detailed descriptions of your security measures, environmental controls, and record-keeping practices. After submission, your application will be reviewed by the regulatory agency, and a field inspection of your facility may be conducted before final approval is granted.
Once the permit is issued, businesses must maintain meticulous records of production volumes, inventory, and distribution activities. Regular reporting to the regulatory agency is required, including tax filings and production audits. Additionally, permit holders must comply with periodic inspections and any updates to the regulations to avoid penalties or revocation of the permit.
Permits can be denied or revoked if the applicant provides incomplete or inaccurate information, fails to meet the security or operational standards, or does not adhere to ongoing record-keeping and reporting requirements. Non-compliance during inspections, evidence of fraudulent practices, or inability to maintain the facility as per safety guidelines are also common causes for denial or revocation.